Your guide to the SMETA audit process
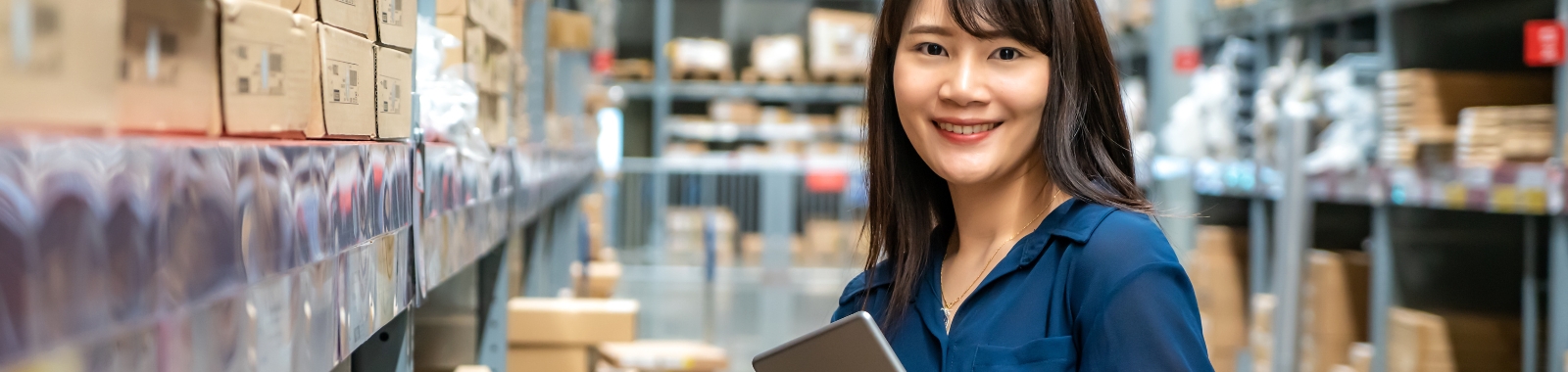

Have you booked or are looking to book your first SMETA audit but you’re still not entirely sure what it is or what the process is? Don’t worry, we have you covered!
Whether you are part of a retailer or brand’s supply chain and they have requested you have a SMETA audit conducted at your site or you simply wanted to understand the social standard performance within your organisation, here is what to expect from the SMETA audit process.
What is a SMETA audit?
As you may already know, SMETA (Sedex Members Ethical Trade Audit) is one of the most commonly used social audits globally and uses Sedex’s social auditing methodology to assess sites and examine the working conditions in an organisation’s supply chain.
SMETA was created to allow suppliers to share one audit report with multiple customers, which helps reduce duplication and audit fatigue. SMETA reports are published in the SEDEX system, ensuring transparent and efficient information sharing.
The audits use the ETI Base Code, which was founded on the conventions of the International Labor Organization (ILO) and applicable local laws and regulations.
SMETA audits can be conducted against either two or four pillars, depending on the needs of supply chains. The two mandatory pillars are Labor Standards and Health & Safety. The two additional pillars of a 4-pillar audit are Business Ethics and Environment.
The latest version of SMETA, SMETA 7, was released in 2024.
Why do I need a SMETA audit?
Third-party social compliance audits in general can help organisations to identify critical issues in their business practices and empower them to mitigate and manage supply chain risks. There are a variety of reasons that you may need a SMETA audit in particular:
- Your customers may have requested it to show that you comply with ethical standards and working with you does not pose a risk to their reputation
- It minimises audit fatigue as you can share results with multiple potential customers, reducing costs and saving time
- It demonstrates that you are committed to a safe and fair working environment for your employees
The SMETA audit process:
Prior to your on-site audit, you should receive and complete a pre-audit information pack that contains a Self-Assessment Questionnaire (SAQ) and all the relevant details for conducting an efficient audit.
Opening meeting
Once the auditor has arrived on-site, they will arrange to have an opening meeting with the management team to detail the format and procedure. The audit is a collaborative process and the involvement of management during the opening interview is a key part of this.
The auditor will clarify the purpose of the audit and the standard or code against which the audit will be conducted, explaining the ETI Base Code requirements and any relevant local laws or regulations. They will also:
- Re-confirm the necessary documents for review
- Obtain a floor plan for the site tour
- Confirm that permission has been given to take photographs
- Check that all staff are aware of the audit and establish that the relevant Code has been communicated to them
- Re-confirm the auditor/audit company’s own Business Ethics policy
- Arrange for employee interviews and explain the process
The audit documents you’ll need
Among the documents that you should pre-prepare for your audit are:
- Documentation of relevant management systems and processes
- Labour contracts/written employment agreements
- Employee handbook and any relevant documents detailing company policies
- A list of all the chemicals and solvents used on the site
- Training records
- Permits, operating licences, certificates of operations, insurance etc.
- Emergency action procedures, evacuation plan and health and safety procedures.
- Time and payroll records for the past 12 months
Site tour
After the opening meeting, your auditor will arrange for a tour of the site to observe the physical conditions and how they compare with the applicable standards, as well as gain an insight into any health and safety issues.
As a general rule, the auditor should be permitted to view all areas of the site and be allowed to set the pace of the tour. The tour also affords the opportunity for more personable conversations with management and employees.
Normal production and operations should continue during a visit to give the auditor a feel for the everyday working conditions and therefore the auditor will strive to move through the site without hindering production.
Interviews
Site tours are an important aspect of a SMETA audit as they allow site practices to be observed, but just as important is information gained from manager and worker interviews.
Interviewing managers can shed light on the procedures and policies the site has in place and allows management to reflect on whether they are being implemented effectively.
Once managers have been interviewed, it’s important for workers to be interviewed both individually and in groups to hear their experiences and personal views on working conditions at the site. The number of workers to be interviewed will correlate with the total employed at the site. It’s also important that no manager or other representative of the employment site is present during these interviews to allow interviewees to speak more freely.
Review of Records
The auditor will also review all documentation previously requested to ensure compliance. The review of records will confirm both information on performance relative the standards and information obtained from the other elements of the audit.
Closing meeting
Once the auditor has completed all fieldwork, including comparison and corroboration of information developed through the audit - a corrective action plan report (CAPR) will be prepared to facilitate a discussion with management during the closing meeting.
The main aim of the closing meeting is to inform and agree the findings of the audit with management and to verify their confirmation of the findings through the signing off of the CAPR and agreed timescales.
The auditor will go through:
- Non-compliances and root causes
- Potential corrective actions for the non-compliances
- A proposed timeframe for correcting issues
What's next?
Once your SMETA audit has been conducted, you should receive your audit report as soon as possible. Within the Eurofins Consumer Products Assurance network of companies, this can be in as little as four working days. Your supplier or customer can also receive a copy of this. The report will also be uploaded onto the SEDEX platform where it can be accessed by entities authorized by the facility.
The SMETA audit report should give a full and accurate picture of the findings and the corrective actions to be taken, where applicable. The SEDEX platform allows facilities to demonstrate improvements by uploading evidence of corrective actions. The corrective actions are independently verified by the original auditor to confirm remediation, For some elements, once the corrective actions have been implemented, a follow-up audit may be necessary.
Ready to book your next SMETA audit? Find out more about how we can help.




© Eurofins Assurance 2025 Personal data protection policy