Quality Control in Garment Manufacturing - The Challenges and Solutions
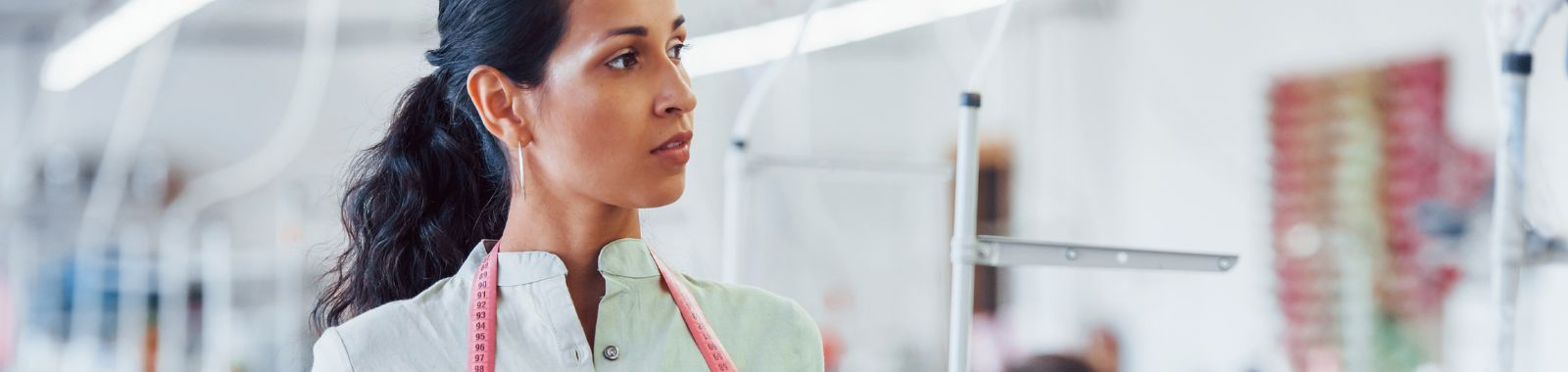

In the competitive garment market, brands need to offer value for money and meet customer expectations without compromising on quality. As a result, there is greater pressure than ever before for apparel manufacturers to have effective processes in place to ensure their clothes are consistently made with the required standards.
Keeping costs low and at the same price point that customers expect from their brand means many manufacturers are now operating at breakneck speed. This results in standard operating procedures (SOPs) being implemented more quickly as well as suppliers being brought on board faster too.
For this reason, it is crucial for any business operating within the garment manufacturing industry to have an effective Quality Control program in place. Without one, issues in quality could jeopardise the business’ brand reputation and relationship with clients, as well as lead to financial loss.
Importance of quality control in garment manufacturing
Quality control in garment manufacturing is an important part in the production process, where the garments are assessed for quality and defects are identified. Quality control (QC) is called often as production inspection.
Quality control in garment manufacturing should take place at different stages in the production process, where the raw materials are inspected before production begins, semi-finished goods and finished goods are also assessed. During quality QC, a number of things can go wrong and could have ripple effect in the entire production line. If the quality of the raw materials is poor, the finished products will very likely be of poor quality; similarly, if the sewing of garment components is incorrect, the final products will be highly defective.
Apart from detecting defects and improving efficiency, the quality control stage is also crucial to maintaining brand integrity. Correcting manufacturing problems at early stageslines can prevent future issues, as well as saving money by reworking or retooling parts that are faulty. If defects are found at the later stages, one could also identify the root causes and improve in next production batches.
Some key checklists of quality control in garment manufacturing
Quality control in garment manufacturing is the process of setting inspection requirement, inspecting product, finding defects, and making repairs or corrections. In general, apparel products are assessed for the following criteria during quality control
Before running the inspection, fundamental step will be to layout the inspection protocol which contains sampling requirements per AQL level, defect list, inspection process, reporting requirements, documentations and other details. Never forget to train the QC personnel and properly aligned so they will be aligned with the expectations laid out in the inspection protocol.
In most garment QC, no matter it is inline inspection or final random inspection, below areas are assessed:
- Colour grade and shades
- Conformity of fabric and hand feel
- Conformity of labels, product tags, barcodes and all other trims and accessories
- Conformity of size measurement and fit comments
- Workmanship
- On-site quality tests such as sewing tests and snap solidity tests
- Fabric weight, etc.
After each inspection is done, consolidating and analysing the QC data for action plan helps drive improvement, and to achieve improvement continuously, action plans should be monitored, assessed and revised regularly to make sure actions are implemented properly, deviation is spotted timely and check if adaptation is needed.
Benefits of a good garment quality control programme
While it is unrealistic to think that a good QC programme can solve all problems in manufacturing, such programme can bring a lot of benefits to the businesses in many ways.
Reduced costs: By identifying problems in early stages of production, manufacturers can make necessary correction to avoid reworking or product rejection. Prevention is always better than cure and this is true in the manufacturing process.
Improve quality: Through the inspection process, manufacturers can identify where defects are occurring in production, look for the underlying causes and make corrections that give long-term effects. As a result, similar issues can be prevented in future production, improving efficiency and cost-effectiveness.
Greater trust: It is very reasonable that buyers tend to work with suppliers with stable and good quality, especially when garments require skillful hands in the manufacturing process. The trust built with existing buyers is great credibility asset to establish connection with new potential buyers and win new businesses.
Reduced environmental impact: Not all defects can be fixed or corrected so faulty goods might end up as waste, which is highly undesirable in the society where ESG are hot topics for the industry. Being right at the first time eliminates extra materials resources needed in reworking/ or fixing, and the possibility of garments ending up in landfills.
Business sustainability: With the costs saved from unnecessary reworking, rejection and other undesirable circumstances, manufacturers can invest in facilities/ equipment upgrades and employee training to boost their competitiveness, promoting business sustainability in the long run.
Conclusion
With the increasing prices of raw materials, energy and labour, implementing a good quality control program can help you ensure the products you sell are of the right quality in a cost-effective manner.
Need help in setting up an inspection programme or upgrading your existing one? Find out more how we can help.
You can download also our Inspection Playbook for a comprehensive garment defect list!




© Eurofins Assurance 2025 Personal data protection policy