Mastering candle quality control: a guide for industry professionals
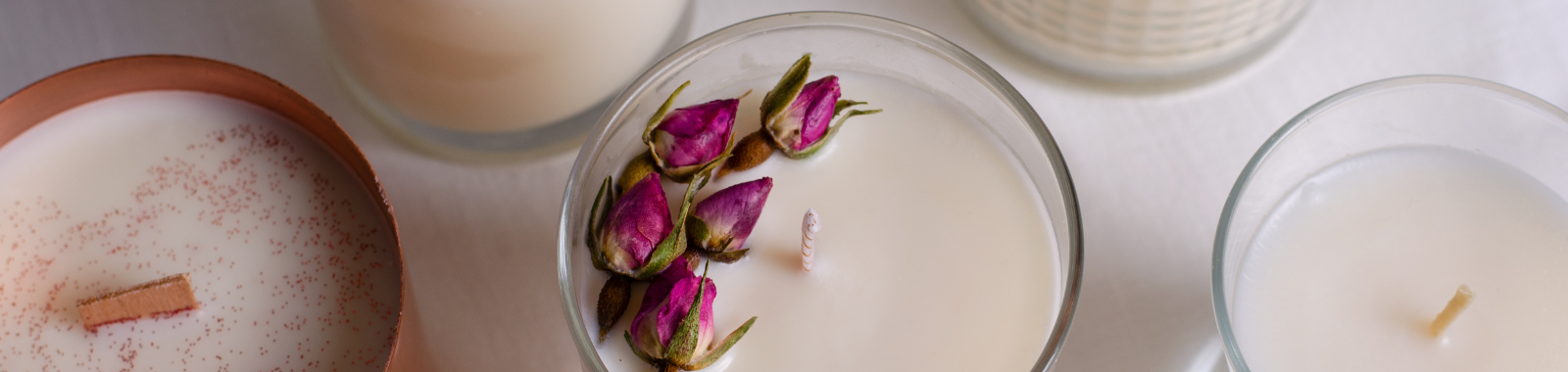

Candle has become a very popular home decoration, lifestyle and wellness product worldwide. Safety concerns however remain high as candle could lead to fire hazards from improper product design, wrong labelling and other factors. Maintaining rigorous quality control in candle can be effective in delivering a product that satisfies both the customers and safety requirements. In this article, let’s deep-dive into the key aspects of quality control in candle inspection and labeling reviews that you can implement for next production.
On-site candle inspection checkpoints
To conduct a thorough quality control of candle’s safety and quality, several critical checkpoints must be addressed during on-site inspections. You can use these checkpoints to ensure that every aspect of the candle meets the desired standards before the product reaches consumers.
1. Dimension checks
Dimensions is the first to be inspected for the candle's performance and aesthetics. Inspectors measure the height, diameter, and wick length to ensure they meet specified requirements. Consistency is crucial for even burning and an appealing product appearance.
2. Burn test
During on-site burn test, candles are lit and their burn characteristics are meticulously monitored and evaluated by inspectors. This process includes assessing flame height, burn time, and any dripping behavior. The aim is to ensure that the candle burns safely, evenly, and consistently, avoiding hazardous or undesirable effects such as excessive flame height or uneven wax pooling.
3. Fragrance evaluation
For scented candles, the fragrance strength and consistency are tested to ensure the scent is evenly distributed and meets expectations. This includes checking for balanced fragrance release throughout the burn cycle, ensuring that the scent intensity is neither overpowering nor underwhelming, and confirming that the fragrance lasts for the expected duration without fading prematurely.
4. Appearance inspection
As like many other products, candles are visually evaluated for their appearance. Cracks, bubbles, uneven surfaces, misaligned wicks or other defects that affect the aesthetic values of candles should be spotted before proceeding to packaging.
5. Adhesion and stability evaluation
Candles must maintain their structural integrity during storage and transport:
- Adhesion: Check the wax’s adhesion to the container. Poor adhesion can lead to separation and compromised product quality.
- Stability: Assess the overall stability of the candle to prevent deformation and damage during handling.
6. On-site safety and performance testing
On-site tests are crucial for assessing the functional performance and safety of the candles, identifying any issues that could compromise their quality or consumer safety.
The tests outlined below are designed to identify potential issues that could impact the candle’s burn quality, safety, and overall consumer experience.
Flame Height Measurement
This is an essential on-site test to assess safety of candles as excessively tall flames can indicate a potential fire hazard. By measuring the flame height, it can ensure candles are safe for consumer use. Flame height shall not exceed 3 inches (ASTM F2417-23 Sec. 4.1) or 75 mm, except tea lights (EN 15493: 2019 Clause 4.3) when measured from the base of the flame to the tip of the flame.
After Smoke Time
This performance test evaluates how long the time smoke is emitted after extinguishing the candle. The procedure involves lighting the candle for one minute and then extinguishing it. The after-smoke time should be less than 15 seconds generally speaking. If it exceeds this duration, the test is considered a fail, indicating a potential issue with the candle's composition or wick.
Soot Build-Up
Soot forms when wax is drawn to the wick faster than it can burn, leading to an incomplete chemical reaction. This performance test involves lighting the candle for 15 minutes and then extinguishing it. Any visible soot build-up on the container wall will be matched to the client's acceptable level based on the sooting evaluation chart. Excessive soot not only affects the appearance but can also pose health and safety risks.
7. Batch consistency
This step enables us to detect any inconsistencies and ensure uniform quality across all batches.
- Uniform quality: Test samples from each batch to ensure consistency in quality, performance, and safety.
- Reliability: Address any variations promptly to maintain product reliability and customer trust.
On-site candle labelling review: regulatory compliance in the US and UK
Proper labelling is not only a regulatory requirement but also a mean of ensuring consumer safety. Key labelling elements include:
- Supplier information: Clearly display the supplier’s name and contact details for traceability and accountability.
- Product identification: Provide accurate details about the product, including its name and specific characteristics.
- Hazard communication: Use pictograms, signal words, and hazard statements to inform consumers of potential risks.
- Precautionary statements: Include safety guidelines to prevent misuse and ensure safe handling and usage.
- Regulatory compliance: Ensure labels meet the standards set by regulations such as the CLP Regulation in the EU and the Fair Packaging and Labelling Act in the US.
Adhering to regulatory standards is essential for legal compliance and market acceptance. Here are some key regulations concerning candle safety for the US and UK/ EU markets, to name just two top markets for reference:
US regulations:
- Fair Packaging and Labelling Act (16 CFR 500): Requires clear labelling with the manufacturer, distributor, or packer’s name and address.
- Country of Origin Marking (19 CFR 134): Mandates proper identification of the product’s origin.
- Lead in Candle Wicks (16 CFR 1500.17 (a)(13)): Prohibits the use of lead in candle wicks to ensure consumer safety.
UK and EU regulations:
- General Product Safety Directive: sets out general principles for the safety of non-food products, including assessment of risks and use of hazard symbols.
- Classification, Labelling and Packaging (CLP) Regulation: Requires detailed hazard communication through labelling.
- BS EN 15494:2019 Candles. Product safety labels: Specifies product safety labelling requirements for candles sold in the EU.
Effective quality control is critical for producing safe, high-quality candles. By thoroughly inspecting the final products, conducting on-site tests, and ensuring proper labelling, buyers and manufacturers can not only enhance product safety and performance but also build consumer trust and brand reputation.
Our team of inspection expert is dedicated to ensuring the highest quality and consistency throughout your manufacturing process. Visit our product inspection page to see how we can support your quality programme.




© Eurofins Assurance 2025 Personal data protection policy