Managing sharp objects safety in ready-made garment factories effectively
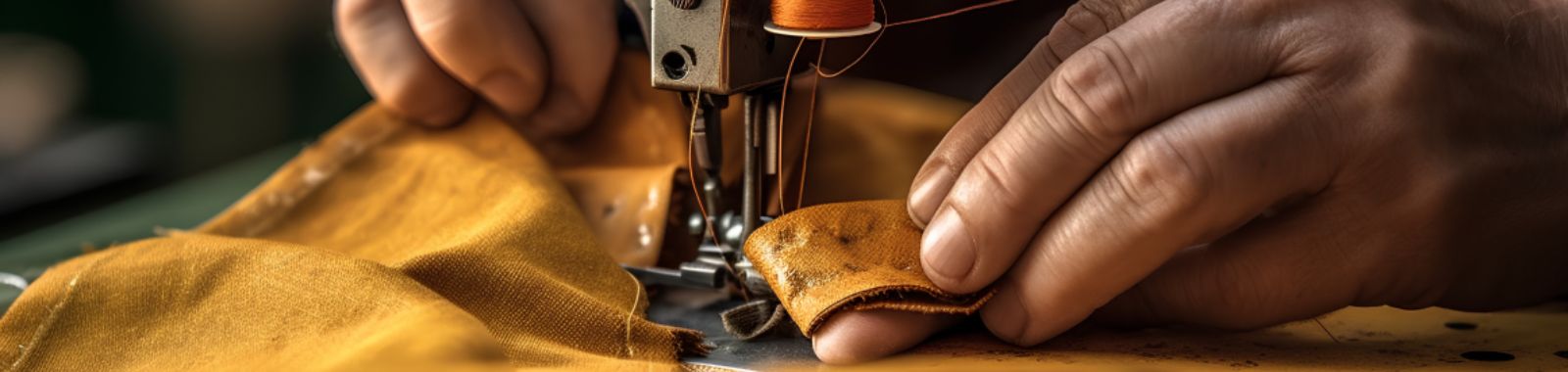

Managing sharp objects safety in ready-made garment factories effectively
Sharp objects management is always a crucial criterion in any ready-made garment factory for both worker safety and product safety compliance purposes. It is thus an important piece in garment quality control policy, as effective management of sharp objects can lead to positive impacts on productivity and efficiency, not to mention fulfillment of product safety requirements.
Common sharp objects failure
Sharp objects are tools or implements that have a sharp edge or point, which can potentially cause injury or damage if mishandled or used improperly. Some common examples of sharp objects in garment factories include scissors, needles, pins, cutters, blades and snippers. In some cases, trim and accessories materials like rivets, studs, snaps and metal buttons are regarded as sharp objects that require good attention in management.
If poorly managed, sharp objects can pose great threats to worker safety and consumer safety, when garment with sharp objects purchased by consumers.
Hazards to worker health & safety
- Cuts and lacerations
- Puncture injuries
- Falls and slips, caused by sharp objects left accidentally on the floors
- Disposal injuries, caused by improper disposal of sharp objects, and workers get injured during waste handling
Hazards to consumer safety
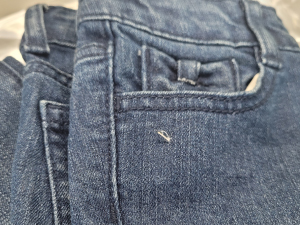
Caption: Broken needle embedded in garment
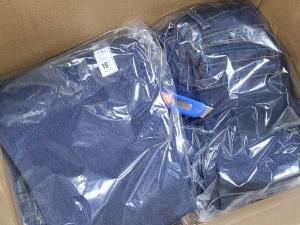
Caption: Cutter found in garment packing carton at retail store
Improving sharp objects management
There are different preventive measures that can be taken with low to medium costs, which will generate greater long-term benefits in enhancing goods’ compliance, building up more trust with buyers and protecting workers.
A. Needles management
Needless to say, needles are one of the few most important tools in garment production for sewing, knitting and embroidery. Needle control should be in place strictly for all processes that involve needle usage, as well as workstations where needles are handled. These workstations should cover storage, production and disposal.
To eliminate the risks of leaving broken needles at garments by mistakes, these steps can be implemented:
- New needles are kept separately from workstations so workers are required to exchange broken needles only at designated areas one by one.
- Broken needle record should be prepared that states the date, time, worker, and line supervisor, with each broken needle attached to each record for tracking.
- In case of lost needles, the production line should be halted and searched to look for the missing needles.
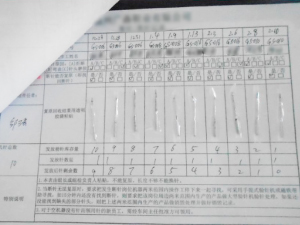
Caption: Broken needle log
B. Other sharp objects
To prevent tools from accidentally leaving workstations or falling into packing cartons, it is recommended to secure all sharp objects to fixtures. Instead of using ropes, which may wear out easily, it is advised to use metal wires or metal chains for installation. This will help ensure the safety of employees and prevent any potential accidents.
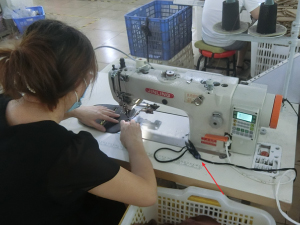
Caption: Sharp tool secured at sewing machine
C. Work environment
A neat and clean environment helps a lot in preventing sharp objects hazards and other accidents, especially at cutting rooms where sharp objects must be present.
D. Metal detection
Metal detection plays a critical role as the last defense in sharp objects management. All goods should be checked by conveyor metal detectors, by production unit or production line. Goods that fail the metal detector should be isolated for search of metal pieces, and are subject to further metal detection after the metal pieces are removed, before they can be packed.
It is crucial to run calibration a few times every day on the conveyor metal detectors to ensure that the machines function properly.
In most ideal situations, metal detection area should be set up in a well laid-out area between final QC and packing so all goods packed and shipped will be in metal-free condition. The packing area should be maintained as a gated metal-free zone that sharp objects are strictly prohibited in the zone. Tools, if needed, are replaced by plastic alternatives.
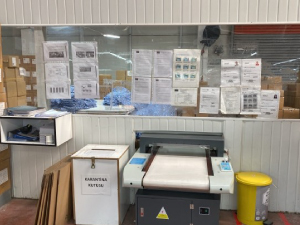
Caption: Packing area isolated from metal detection area
E. Staff training
For best execution of sharp object management policy, it is imperative that workers adhere to all workflow requirements. It is crucial for employees to recognize the potential risks associated with sharp objects, both to their own safety, as well as to consumers and the factory. By understanding these negative impacts, workers will naturally exercise greater vigilance in their actions. To ensure this understanding, workers should be thoroughly briefed on all policies and procedures regarding the management of sharp objects.
Eurofins CPA offers full suite of inspection services and inspection training. Contact us anytime for a proposal.




© Eurofins Assurance 2025 Personal data protection policy