Implementing a quality management system for consumer goods manufacturing: key steps and best practices
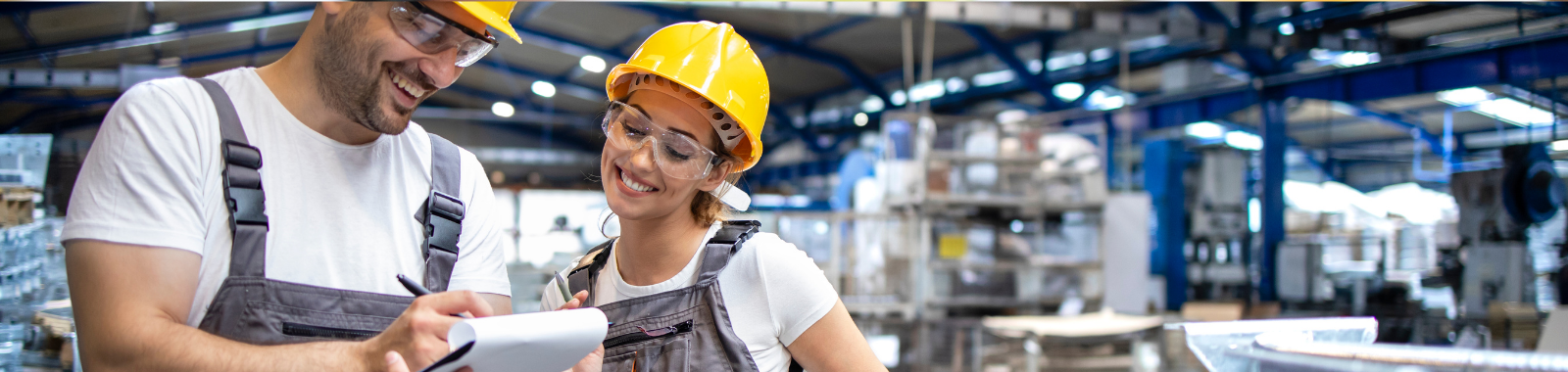

Quality and safety in products are core factors for a business to stand out in domestic and worldwide competition. A well-established quality management system (QMS) at your manufacturing site will be key to such success, enabling you to better manage product quality and enhance efficiency. In this article, we will break down how businesses can implement quality management systems for consumer products manufacturing.
Adopt a process approach
There are several approaches to implementing a Quality Management System (QMS), but regardless of the chosen method, it should be seamlessly integrated into everyday business operations. One of the most prevalent practices in the industry is to adopt a process-oriented approach that utilizes the “Plan-Do-Check-Act” (PDCA) methodology alongside risk-based thinking. This combination is essential for developing, implementing, and continually improving the effectiveness of a QMS.
Leadership and commitment
Quality is not the responsibility of a single person, production line or functional area in a company. It requires all parties’ participation from top management to production line operators. To successfully implement QMS, senior management’s leadership and commitment are essential, not only for resource investment but also for active and direct involvement in the QMS operation. In addition, a working group composed of management from different functions is also indispensable to drive QMS implementation and coordinate among all parties.
Step-by-step implementation
Having discussed mindsets and approaches, we will look at several key steps in QMS implementation that ensure quality and compliance in your product manufacturing.
1. Identify requirements: The company should understand customers’ expectations and identify applicable statutory and regulatory requirements which will allow clear analysis of internal and external risks and opportunities of such production. This will help prepare the overall QMS strategy and roll-out plan. When it comes to product manufacturing, these are some fundamental regulatory requirements that should be taken into consideration:
-
- Garments and footwear: Restricted chemical substances, labelling, and safety standards such as flammability.
- Furniture: Compliance with safety standards from mechanical hazards and the use of non-toxic materials.
- Toys: Adherence to strict safety standards for small parts, chemical substances and markings.
2. Define quality policy and objectives: Businesses should then define and develop quality policy and quality objectives that are consistent with the company’s overall business strategic direction and operating environment. The quality policy, written by senior management with inputs from the working group, serves as a guide for management actions. The quality objectives should be determined according to the SMART (Specific, Measurable, Achievable, Relevant, and Time-Bound) approach.
For a toy manufacturer, for example, an objective might be: "Reduce the rate of product recalls by 20% within the next year through enhancing material safety testing procedures".
3. Map processes: After policies are laid out, businesses should determine and map the manufacturing processes including activities, associated resources, and controls necessary to transform inputs to desired outputs. You can first start with on-site studies, draft the process flow diagram, and identify critical control points, followed by on-site verification. Both process effectiveness and efficiency are critical; exclude any non-value-added activities to stay streamlined and focused.
In a footwear manufacturing site, essential processes will cover materials selection, cutting, sewing, lasting, assembly, finishing, packaging.
4. Document system: While formal documents are not strictly necessary for QMS, they help ensure consistency over time. A general document system consists of 4 layers:
-
- Quality manual: Provides the scope and overview of the QMS and interactions among different processes.
- Procedures: Define operations of different processes.
- Work instructions: Describe steps for specific activities.
- Records: Retain operational and performance monitoring data as evidence of conformity.
5. Document control: Companies need to define document control mechanisms to ensure documentation used is the most up-to-date version. Each document should have a unique identity with version and effective date, written in a language easily understood by users. Documents should be approved by authorized approvers, with revision histories maintained. A formal document distribution management system is recommended to issue new versions and remove obsolete ones. Records must be managed and controlled like documents, generally kept longer than the product’s service life, and at least 3 years.
Resources allocation
Make sure to allocate resources to achieve quality goals by optimizing the workforce with necessary personnel, knowledge, and competency. Ensure a suitable work environment and facilities, such as adequate monitoring equipment, to support effective QMS implementation.
Launch and communication
After the setup phase, it is critical to launch the QMS with clear communication to employees at all levels. Preventing product and process problems is preferable to taking corrective action after production. Long-term actions are crucial to maintain effectiveness:
- Regularly monitor, analyze, and review quality performance to identify weak points that need improvement.
- Validate the implementation, effectiveness, and efficiency of the QMS at regular intervals.
- Common methods include periodic quality reviews, quality audits, management review meetings, etc.
- Optimize the system based on review results. Address any identified areas for improvement through the CAPA system (corrective and preventive action system).
By focusing on these industry-specific aspects, your QMS implementation will provide valuable insights and guidance for consumer goods manufacturers looking to implement or improve their quality management systems. A successful QMS can bring enormous benefits to a business, including
- Ensuring products consistently meet customer and regulatory requirements
- Increasing competitiveness
- Reducing quality costs and increasing profitability
- Enhancing customer satisfaction and loyalty
- Facilitating internal knowledge transfer
If you are not sure where to begin with to implement your own QMS, or want to examine a new supplier’s technical competency before placing a new order, visit our technical audit page to learn more about how we review and assess factory quality systems in bespoke solutions.




© Eurofins Assurance 2025 Personal data protection policy