How to effectively build and implement a chemical purchasing policy
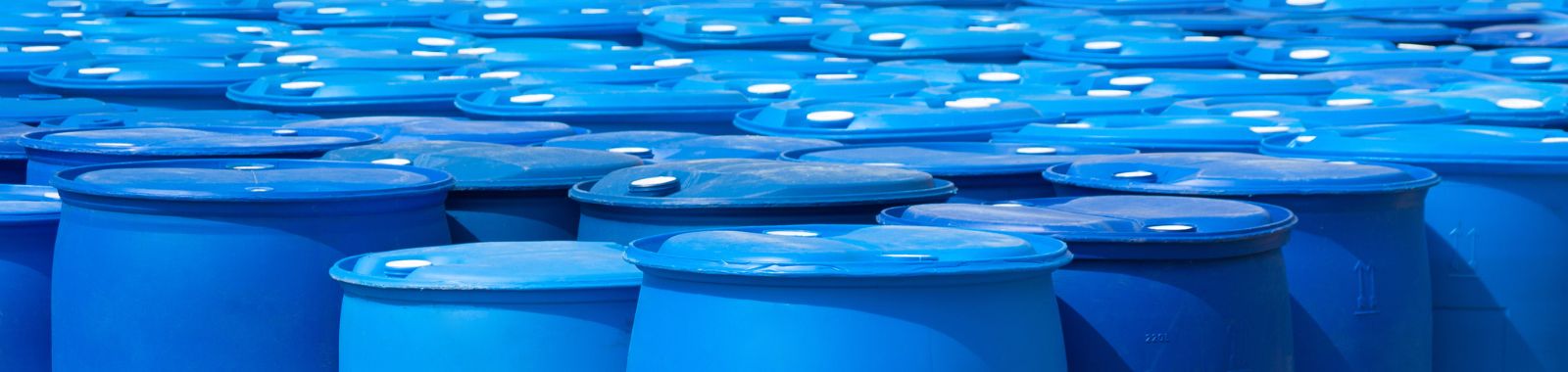

We all know that proper chemical management policies and procedures are crucial for the textile industry, in order to effectively monitor compliance with regulations on restricted substances within a complex supply chain. In particular, alongside the much-discussed MRSLs (manufacturing restricted substances list) and RSLs (restricted substances list), a well-defined chemical purchasing policy should be a key part of your strategy for controlling and phasing out any harmful chemicals from production.
Based on buyers’ requirements and established at factory level, a chemical purchasing policy states precisely the requirements with which chemical suppliers are expected to comply in order to control the use of restricted chemicals in the supply chain.
Establishing a good chemical purchasing policy
Most importantly, the managers in charge of the chemical management system (CMS) must ensure that the chemical purchasing policy covers all obligations for chemical suppliers, which should include:
- Acknowledging their understanding of the RSL and MRSL policies
- Acknowledging their understanding of the RSL/MRSL testing requirements and list of approved laboratories
- Committing to transparency about the chemical products purchased (and in particular, the ingredients/composition of those chemical products)
- Committing to providing up-to-date and complete Safety Data Sheets (SDS) and Technical Data Sheets for each chemical product as per the Globally Harmonised System (GHS) requirements.
- Committing to delivering chemicals with accurate and complete labels (in compliance with the GHS system).
- Committing to providing evidence of MRSL/RSL compliance for each chemical product sold (through certificates, test reports, etc.)
- Committing to continually improving the responsible manufacturing of chemicals (through internal quality control procedures, robust procedures for generating SDSs, screening raw materials, etc.)
Once the standard for purchasing chemicals is set, the managers in charge of the CMS, along with the purchasing department representative, can prepare:
- A list of approved chemical suppliers based on their capacity to comply with the requirements mentioned above, as well as other criteria in terms of responsible upstream chemical management, and
- A list of approved chemicals based on the conformance levels of compliance evidence provided
Want to learn more? Take a look at our chemical management online learning.
What is a Safety Data Sheet?
A Safety Data Sheet (SDS) is a document which compiles the properties of a particular chemical product and provides information on how to use and store it safely, and what to do in an emergency. An SDS will also contain important information to ensure the safety of workers handling the chemicals.
What is the GHS?
The GHS is the Global Harmonised System of Classification and Labelling of Chemicals. Developed by the United Nations, the GHS is widely adopted by various industries in classifying, identifying and documenting chemicals.
We offer chemical management audits to support your compliance effort. Find out more details here.




© Eurofins Assurance 2025 Personal data protection policy