Enhancing denim quality: best practices for denim stitching and washing
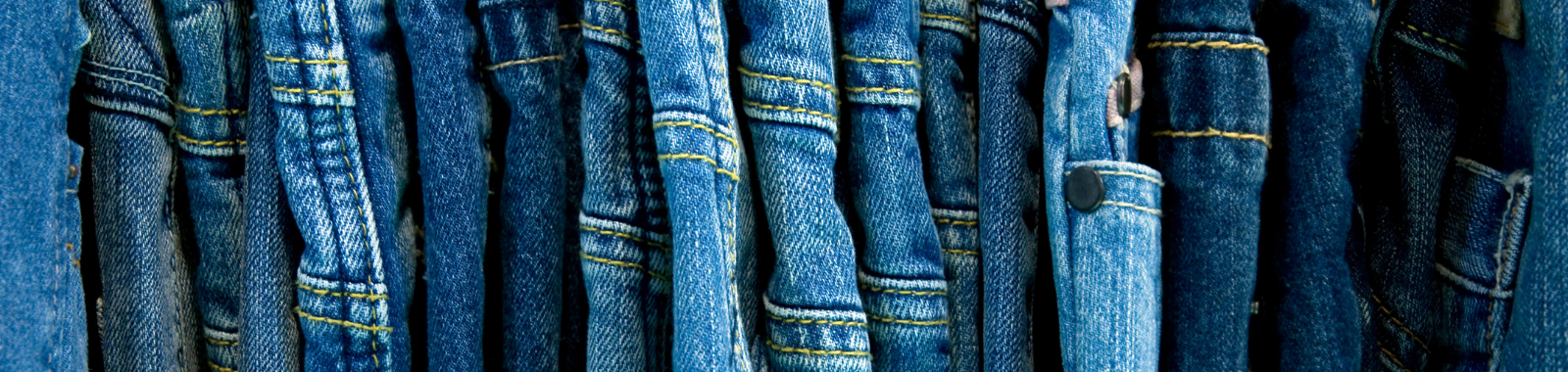

Denim has been popular among different consumers since it came to the market several centuries ago. Whether in jeans, jackets, dresses, skirts, or other styles, quality management in denim production is essential for producing high-quality products. Effective quality control ensures that quality denim products meet high standards, reduces waste, minimises rework costs, and increases productivity. This article focuses on key aspects of quality management in two crucial stages of denim manufacturing: denim stitching and denim washing.
Best Practices in quality assurance for Denim Stitching
Stitching is vital for the durability and aesthetic appeal of good quality jeans and other denim products. This part of the process plays a significant role in determining the strength and finish of high-quality denim jeans. These are the key points to consider when you look for maintaining a good quality assurance policy on denim stitching:
- Fabric Evaluation: It is imperative that the manufacturer employs an effective fabric evaluation process so that rejection due to denim fabric defects is minimised.
- Shrinkage and Shade Management: Manufacturers must make sure that proper shrinkage tests are done, and the results are correctly applied at the time of plotting the markers. Also, inherent shades from the mill are identified, grouped, and managed in production accordingly.
- Inline Inspections: One of the most crucial parts in apparel manufacturing quality is structured random inline inspections (SRIs). SRIs play a pivotal role in identifying defects at the workstation and are also a source of quality data of defects for continuous improvements.
- Process Control and Validation: Controlling the defects at the needle point by identifying the ‘assignable cause’ is the objective here. With precise root cause analysis and effective deployment of corrective actions, defects per hundred units can be substantially reduced. Employ rigorous process control measures to maintain consistency throughout production, especially since there are usually many components to sew together for one denim product. Attention to denim details and denim construction is crucial.
- Critical Stations: Deployment of specialised check points at all critical stations in stitching to make sure that all critical processes are defect-free.
- Offline Checking: Perform a thorough measurement of garments before washing to identify defects that can be corrected and confirm correct application of shrinkage.
- Defect Data Collection: Systematically gather data on defects to facilitate statistical process control and drive continuous improvement initiatives.
- Product Safety: With various product safety regulations in different markets, both buyers and suppliers are expected to make sure that products fulfill regulatory requirements and are safe for consumers, especially for children's wear.
From our experience, factories can adopt tools ranging from traditional checks to digital tools to ensure consistency in stitching and monitor progress and statuses effectively.
Nevertheless, regardless of factory sizes, having a comprehensive quality management system that consists of periodic data analysis and continuous improvement plans, coupled with proper staff training, is a fundamental approach to good quality assurance.
Best Practices in quality assurance for Denim Washing
Washing significantly impacts the final look, feel, and colorfastness performance of denim. Among many different washing techniques for high quality jeans such as stone washing, enzyme washing, and acid washing adopted, it is thus more essential to have a proper quality policy so all processes will go as they are expected. Below are key points to consider when planning around denim dyeing:
- Wash Recipe Management and Control: Ensure consistency in the recipe transition from sampling to bulk and control how all the wash recipes are managed and kept.
- Wash Load Management: Managing wash load is important to ensure that washing is done shade-wise and washing recipes for denim are trimmed accordingly.
- Control Procedures at the Washing Machine: Stringent control measures are necessary to make sure that proper control is in place. This is to ensure that correct disbursement of chemicals and other controlling parameters are effective.
- Periodic Shade Review and Measurement Controls: Regular assessment of shades and post-wash measurements are crucial; it requires a constant monitoring process to ensure consistency.
- Trial Load Approvals: Verify quality through trial loads before full-scale production.
- Chemical Store Management and Housekeeping: Current global and local environmental laws have created regulatory frameworks that all manufacturers should have policies and procedures in place defining chemical store management and housekeeping to stay compliant.
In order to fulfill the above, factories leverage multiple initiatives including recipe library and database, transition calculations and records, shade and measurement review, and approved shade bands on the production floor.
Similar to previously discussed denim stitching quality management, a robust chemical management system is required for the compliance of these critical materials.
Contact us today to learn more about our premium denim quality management services and how we support you to improve denim quality with gap analysis and customized solutions.
Further readings




© Eurofins Assurance 2025 Personal data protection policy