How to build an effective product inspection protocol that fits your needs?
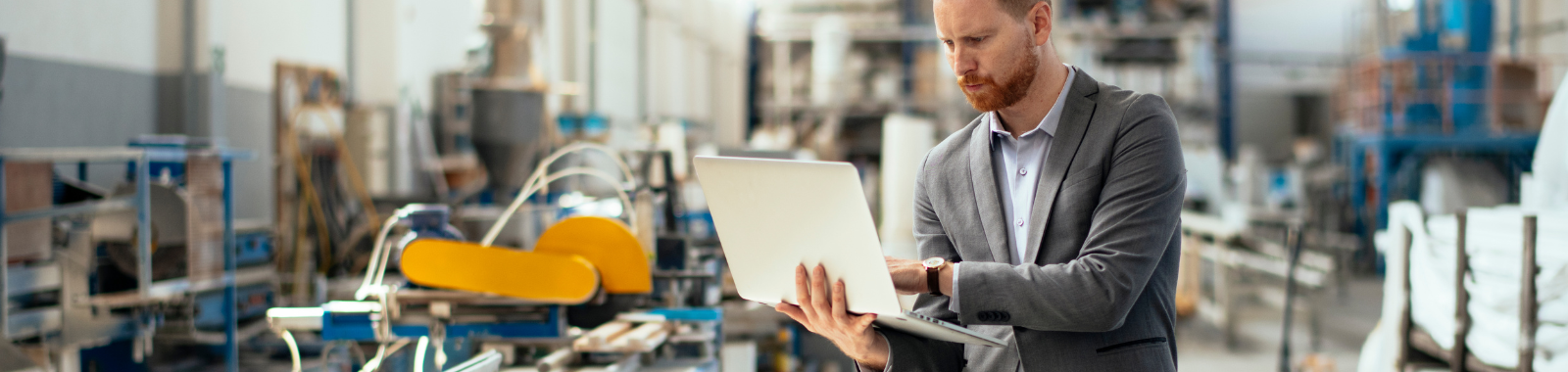

Conducting product inspection is crucial for ensuring that goods meet quality standards and safety requirements before reaching consumers, reducing cases of complaints and returns. By following well-defined inspection protocols, companies can identify and address potential defects, deviations, or safety concerns effectively. However, developing such protocols will require good understanding of the market requirement and inspection knowledge. In this article, we are laying out key notes in inspection protocols building that can fit in different product categories.
Risks of Inspection Without proper Inspection Protocol
Although in most scenarios, inspection is done on a random sampling basis, this does not mean it can be done randomly. Absence of proper inspection protocol and control system could lead to different issues.
Risk 1: Subjective judgement
Without a clear set of guidelines, inspectors may rely on personal judgement, which can vary significantly from one individual to another. This would lead to different conclusions about the same inspection.
Risk 2: Missing out product-specific quality requirements.
Each product category’s manufacturing process in general has distinct quality standards and criteria tailored to the specific requirements. For instance, the manufacturing of garment demands workmanship alignment, while electronics manufacturing emphasises precision and functionality. Customised inspection protocols play a crucial role in ensuring that the unique quality standards of each product and process are met.
Risk 3: Inefficiency
Conducting inspections without an appropriate protocol could be inefficient and lead to a waste of resources. Inspectors may spend unnecessary time and effort on non-critical aspects or perform redundant inspections, leading to inefficiencies and increased costs.
Risk 4: Need for re-inspection
Inconsistent inspections often result in the need for re-inspection or additional checks to verify findings, creating higher costs and possible delays in shipment timelines.
Risk 5: Overlooking important aspects
Without predefined criteria and procedures, inspectors may overlook or fail to assess critical quality criteria, increasing the chance of defective or unsafe products reaching customers which cause dissatisfaction and potential safety concerns.
A poorly designed inspection protocol undermines the integrity and effectiveness of the whole inspection process, leading to inconsistent quality, increased costs, regulatory risks, and customer dissatisfaction. It is thus fundamental to design the inspection protocol carefully to best utilise such quality management tool.
Key notes to building an effective product inspection protocol
In a nutshell, an effective inspection protocol should be clear, comprehensive, standardised, and specific to guide all inspectors involved on aligned assessment criteria, inspection processes, checking points and defect evaluation so the results are benchmarkable and objective.
To create such protocols, you have to explore and elaborate upon each aspect of the inspection, from understanding customer preferences and defining critical quality attributes to implementing inspection criteria.
- Understand Customer/ Market Requirement of the product
Begin by thoroughly understanding the specific requirements, preferences, and quality standards of the customers and the market trend against your brand’s proposition. This step could involve analysing precious feedback, conducting surveys with consumers, or directly communicating with customers to gather insights of the product being inspected. Running industry benchmarking exercise to find out how the same products by your competitor perform is also a good option.
- Identify all quality attributes
The next step is determining all the quality attributes in term of dimensions, material quality, functionality, performance, safety features, and aesthetic appearance. We usually achieve this by listing out all possible defect one product could have and categorise defects into critical/major/minor according to findings from point 1.
- Define Inspection Criteria
A lot can go wrong with your product, be it a wrong label, incorrect hang tag or missing packing materials. Here are fundamental aspects to take into account when developing the inspection protocol:
- Labelling
- Workmanship (appearance by visual, hand feel, smell, construction, materials)
- Packing and assortment
- Product conformity (style, materials, colour, etc.)
- Onsite tests (carton drop test, assembly, functionality, barcode scan, measurement, weight, etc.)
- Confirm AQL Sampling Plans
Confirming sampling plans to determine the quantity of units to be inspected from each production batch is one tricky step. Being too tight it could incur unnecessary manpower and cost, while being too loose the quality could slip. Different sampling plans are adopted according to various product categories and expectations. Sampling plans should be statistically valid and be based on factors such as production volume, product complexity, acceptable risk levels and previous production defect rates. Nowadays, sampling plans are mostly made with reference to Acceptance Quality Limit (AQL) and the common AQL range of general inspection levels is 2.5 to 4.
Further readings: Explaining Acceptance Quality Limit (AQL) for product inspection
- Consider Regulatory Compliance
If applicable, ensure that your inspection protocol complies with relevant industry standards, regulatory, and certifications requirements. This is especially important for products subject to safety, health, or environmental regulations. For example, the special safety requirements on childrenswear in EU and US markets.
- Regular Review and Improvement
Regularly review and evaluate the effectiveness of the inspection protocol based on feedback, inspection results, and customer satisfaction. To achieve this, you will need to set up KPIs related to quality covering defect rates, customer complaints, return rates, etc. Insights from good inspection protocols will form a solid backbone for a robust inspection programme that drives continuous improvements.
Tailored inspection protocols are essential for meeting the distinct quality standards of different production processes. By implementing customised inspection procedures, companies can effectively ensure that products comply with specific quality, safety, precision, and functionality requirements, ultimately ensuring satisfaction at end consumers.
Running inspection programme in-house is not uncommon, but engaging a knowledgeable third-party inspection company allows you better flexibility in resources planning and business continuity for the long term. Our experts in Eurofins possess in-depth knowledge of industry-specific standards and best practices. Their technical expertise and experience from working with a variety of customers and industries can help in identifying critical inspection points, identifying potential risks, effective sampling plans, and adherence to regulatory standards efficiently.
Read more about how we can support you in product inspection and contact us for your inspection proposals anytime.




© Eurofins Assurance 2025 Personal data protection policy