Bringing clarity to the environmental performance of factories
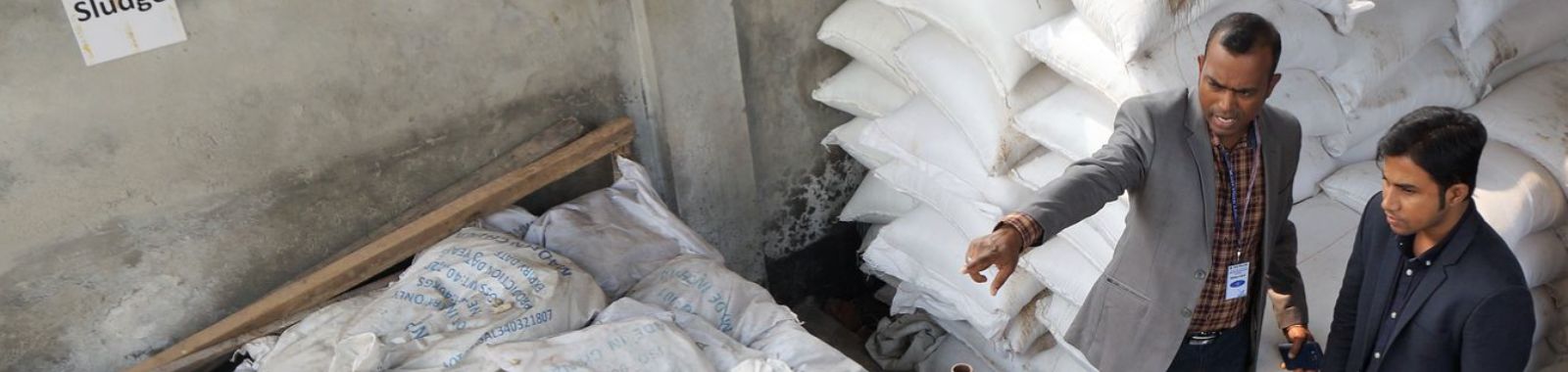

A version of this article previously appeared in the June issue of Ecotextile News
In the past decade, the textile and footwear industry has spared no effort in identifying the key considerations for the environmental performance of the supply chain, particularly with downstream suppliers, and implementing the measurements required to drive continuous improvement.
An on-site environmental audit is one such way to effectively drive actionable insights and improvement. Three major topics addressed during an on-site audit are: wastewater/effluent treatment plant management, chemical management and hazardous waste management.
Wastewater/ effluent treatment plant management
Effluent treatment plants (ETPs) exist mostly with suppliers in lower tiers such as wet processing facilities, dyeing mills and tanneries and they form a fundamental part of the entire supply chain.
For effective wastewater treatment, the ETP capacity must be adapted to the volume of wastewater discharged by the facility. Water flow meters should be installed at the source of incoming water used in the production, at the ETP inlet and ETP outlet points to verify if the volumes are consistent. Any important gaps in measurement can indicate a risk of bypass lines or a risk of ETP is under capacity.
Equally important is the on-site observation of a water sample collected from the ETP outlet point. Besides the test results, naked-eye observations can reveal issues with the ETP such as bad odours, high turbidity and persistent foam.
Proper chemical management
Having robust and proper chemical management helps better mitigate hazardous chemical substances entering production. It also safeguards the health and safety of workers with possible contact with chemical substances.
Chemical products should be stored in dedicated areas away from the production area, with restricted access. Only staff that have received relevant training should access and handle chemical products. Cleanliness, good ventilation, no exposure to sunlight and proper electricity connection/wiring are all essential for a safe chemical storage area. Trained staff should arrange the segregation of incompatible chemicals in the storage area carefully. Putting incompatible chemicals together could lead to high risks of fire, explosion or leakage of toxic gases.
The department in charge of chemicals purchasing should ensure all chemical products are supplied with the correct Global Harmonized System (GHS) label and complete and up-to-date Safety Data Sheets.
Solid and Hazardous waste management
Empty chemical drums and sludge are two of the hazardous solid wastes from textile and footwear production and require extra caution in their disposal to prevent persistent contamination.
The drums must be temporarily stored in a designated area away from production sections with a concrete-paved ground surface and shelved roof to avoid groundwater and soil contamination. Similarly, sludge is required to be well bagged in water-shield packing and stored in an isolated environment with a hard-surfaced floor and ceiling.
Waste contractors should be selected based on their practices to dispose of/treat hazardous waste. The facilities should expect transparency on waste disposal methods from the waste contractors.
Textiles and footwear manufacturing has often been linked to heavy pollution. The onus is now on brands and retailers to shift this perception with more robust oversight of practices impacting environmental performance.
This is where the environmental audit services offered by the Eurofins Consumer Products Assurance network of companies can help. Our experts have significant chemical knowledge, audit know-how and field experience, enabling them to generate an audit that provides a comprehensive picture of a manufacturing site’s environmental performance.




© Eurofins Assurance 2025 Personal data protection policy