Reducing unwanted streak marks on jeans significantly
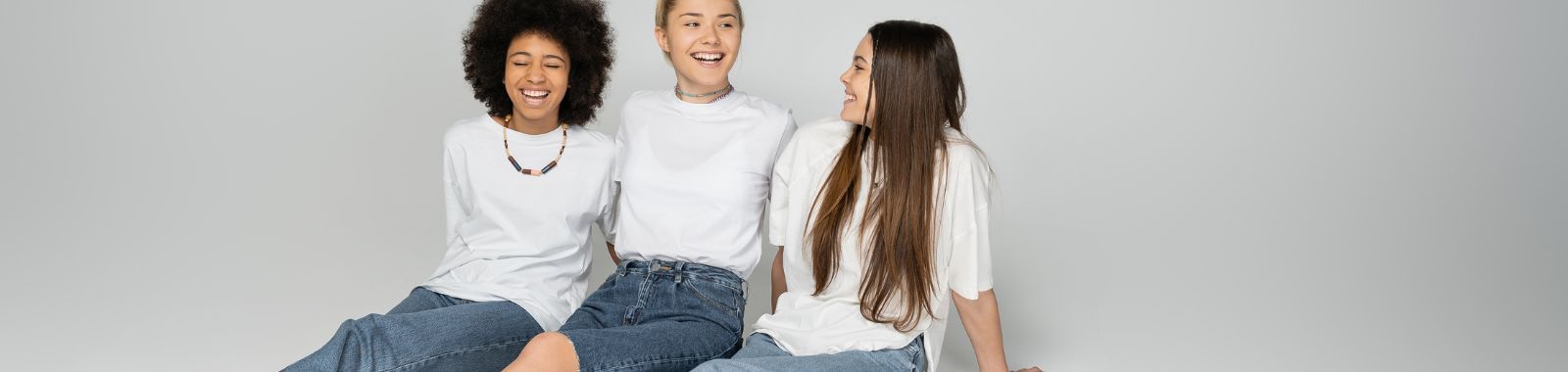

Achievement highlights
Reduced problematic jeans with unwanted streak marks from 10 – 15% to less than 1% and 0.5% in process and in bulk respectively.
What was the issue?
Unintended streak marks were found on jeans after washing at the brand’s garment factory in Bangladesh, causing quality issue to the delivery of this order of 1.1 million pieces.
On a rough examination, 10% to 15% of checked jeans were found to carry such streaks marks. Had the goods arrived on the market, one could imagine a potentially high return rate from consumers dissatisfied with the jeans they purchased.
Caption: Photos of unintended streaks on jeans
Why did the issue happen?
Our QA experts carried out a root-cause analysis to uncover three underlying causes after the troubleshooting visit:
- Washing recipe was not followed properly
Different temperatures ranging from 45°C to 60°C were required during different stages of the wet processing, as stated in the washing recipe. However, instructions were not well followed, and water temperatures were set too high for this fabric, causing shrinking and leaving creases and streaks on the jeans. In some scenarios, for example, the temperature was set at 50°C to 60°C, while the correct degree was 45°C. - Poor housekeeping during washing process
For optimal results, 130 pieces of jeans could at most be processed at once but more than 140 pieces were processed together by workers. Also, washed jeans were left unattended for prolonged period. After washing, the goods were left idle for 6 to 8 hours before they were sent to next processing step. The storage space was badly set up as no shelves/ baskets were used to store washed jeans in small batches to avoid exerting too much pressure on the jeans at the bottom. FIFO (first-in-first-out) arrangement with clear documentation/ labelling was missing also to process washed jeans timely and effectively. The failure in washing operations has caused formation of permanent creases and streaks as jeans were dried up in improper conditions. - Improper/ Inadequate in-house QC
Washing QC and garment QC at factory were not executed properly. Some defective goods were approved and triggered the quality alarm at the customer’s side.
Caption: photos of jeans under poor housekeeping
How did we fix it?
Targeting the four problems identified, our QA-QC Team has made below suggestions which improved the situation significantly.
Solution for wrong washing recipe and poor washing housekeeping
Washing recipe and process were both adjusted. Temperatures were turned to correct degrees as listed on washing recipe. Workers were given new instructions to handle the jeans correctly before and after washing to prevent streaks formation. Training to workers was provided to make sure new process was followed.
key point: dry the jeans for 5 minutes from previous step before washing
Key point: dry the jeans for 5 minutes from previous step before washing
Key point: wash 120 pieces maximum each time
Solution for improper in-house QC
In-house QC checks and reports were monitored to ensure quality checks were first done properly at factory. Capability building was a key part to improve from root so in-house QC training was done around incoming materials control after washing with controller SOP updated. A clearer policy on defect sorting was reinforced also so rejected pieces are cleared from stocks promptly.
As a third-party player that commits to bring assurance to our customers, Eurofins’ teams made daily visits to the factory to verify in-house QC performance against Corrective Action Plan (CAP) log. Random visits were made also to the washing section to pay extra attention to the problematic areas.
What were the results?
With the effort spent of all parties, the failure rate has been greatly reduced from 10% - 15% as mentioned in the beginning, to less than 1% and 0.5% for in process and in bulk respectively.
Needing a hand in your garment and textile production? Check out how our QA-QC Programme for Apparel and Garment Industry can help!




© Eurofins Assurance 2025 Personal data protection policy