Product final inspection - how is it done?

When an inspection report arrives in your inbox, have you considered the steps it took to get there? How do our inspectors handle your inspection requests? Let’s take a closer look at the five key steps in final product inspection.
What is final product inspection?
Generally speaking, final inspection is carried out when the production process of a batch for a specific purchasing order (P.O) is completed 80% or more. As a buyer, final inspection provides you with critical insights on the quality your consumers should expect when they bring your product home. Depending on the results of the final inspection, merchandisers and QC may accept, reject or negotiate specific aspects of the goods with suppliers.
Final product inspection: Step One – Picking
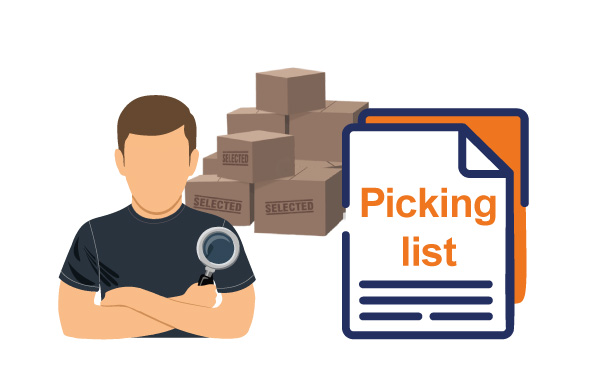
Picking refers to randomly selecting product cartons for inspection from finished and packed cartons.
This process begins by making sure that the packing list matches the number of cartons on site. Our inspectors prepare a picking list and select cartons respectively in line with the lot sampling size established by buyers. Packers from the factory pick and transfer selected cartons to an inspection area under the supervision of inspectors. Cartons are then opened by packers in preparation for the next step, again, under the supervision of inspectors.
Final product inspection: Step Two – Packing
At this stage, our inspectors check the packing conditions of the selected cartons against the buyers’ specifications. This includes:
- Packing
- Shipping marks
- Quantity
- Packaging e.g. polybags or other materials
- Logistic stickers
- Barcodes, etc
When carrying out packing inspection, we provide specific results (Pass/ Fail/ Reservation/ Not applicable) with comments for each specification checked.
Final product inspection: Step Three – Conformity and On-site Test
The next step of the inspection process is to check the conformity of the goods. Using product samples or technical files provided by the buyers, our inspectors examine various quality parameters of the selected goods.
For garment products, we check:
- Colour grade and shades
- Conformity of fabric
- Conformity of labels, product tags, barcodes and all other trims and accessories
- On-site quality tests such as sewing tests and snap solidity tests
- Product weight
- And a lot more!
For electronic products, we check:
- Style
- Functionality
- Print and logos e.g. CE Mark logo, RoHS logo
- User test
- Accessories such as charger, cable and earplugs
- Parts and components
- User manual
- And a lot more
For furniture, we check:
- Style
- Assembling test
- Colour resistance
- Smell test
- Static loading test
- Product stability test
- And a lot more!
Apart from assessing the products, we examine the quality of the carton boxes transporting the products, through carton drop testing and carton humidity testing, so buyers can be assured of product safety during the entire shipment and delivery process.
Final product inspection: Step Four – Workmanship and Measurement
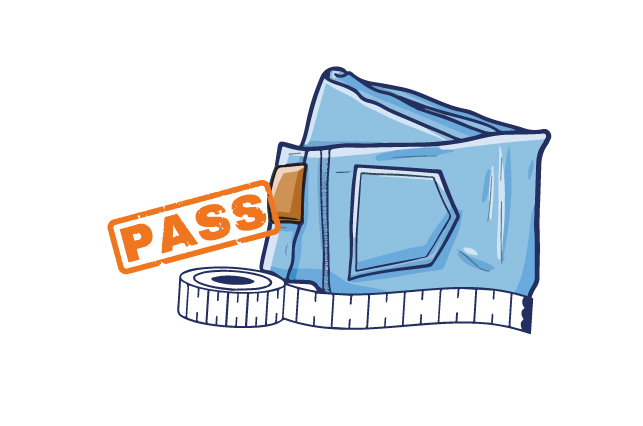
We examine products inside-out to carefully assess workmanship, from the inside seam of a pair of pants, the screw base of a lighting item, the switch of an electrical toy or the handle of a drawer in a closet.
We examine products inside-out to carefully assess workmanship, from the inside seam of a pair of pants, the screw base of a lighting item, the switch of an electrical toy or the handle of a drawer in a closet.
Measuring the sizes of products is very important too, particularly for textiles products which are cut and sewn together piece by piece.
Similar to the packing assessment, our inspectors give Pass/ Fail/ Reservation/ Not applicable results on workmanship and measurement with relevant comments on each specification checked, in line with the AQL (Acceptance quality limit) agreed with buyers.
At each inspection, our inspectors always identify most critical defects found in the products and label them with defect stickers for the buyers reference. Upon buyer request, we can also identify products that have passed inspection with pass stickers, or seal and send defect products to buyers.
Final product inspection: Step Five - Closing
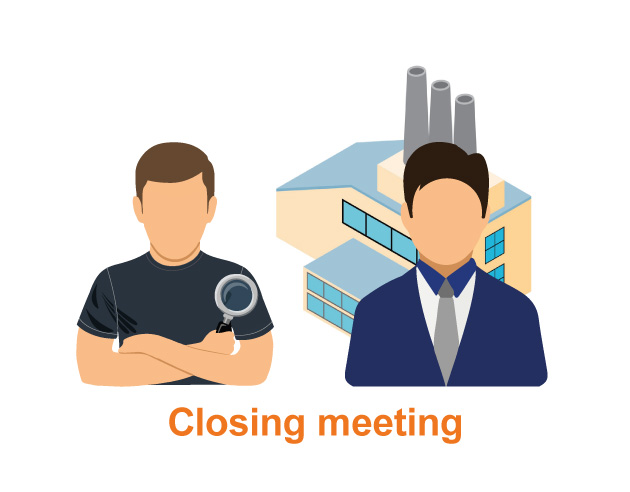
When product inspection is complete, our inspectors supervise the repacking of goods by packers or factory workers. Following that, inspectors hold closing meetings with factories where in some cases, signed copies of inspection drafts are shared with factories upon buyer agreement.
When product inspection is complete, our inspectors supervise the repacking of goods by packers or factory workers. Following that, inspectors hold closing meetings with factories where in some cases, signed copies of inspection drafts are shared with factories upon buyer agreement. We have now covered the key steps in final product inspection. It might seem straightforward but in reality our inspectors often encounter unforeseen issues like incomplete product production, power failure in factories, or difficult weather conditions.
Next time you review your final inspection report, you can be assured of the stringent process followed by our frontline team to safeguard your product and your brand’s reputation!




© Eurofins Assurance 2025 Personal data protection policy