How to implement a corrective action plan
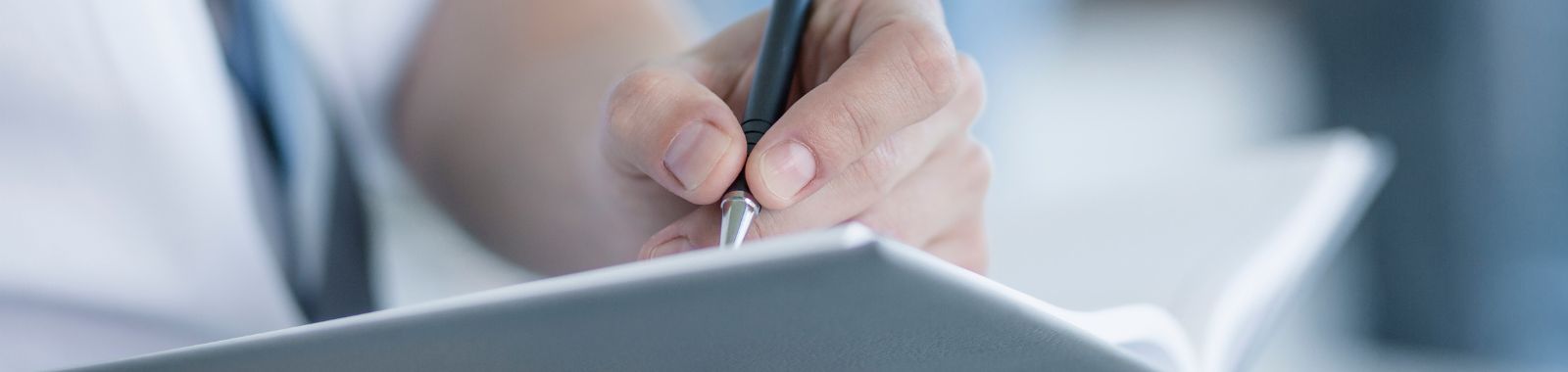

Once a factory assessment has been completed by your third-party auditor and any social, technical or environmental compliance issues have been raised, your business is likely to receive a corrective action plan at the end of the audit. The full report can take several days to be completed.
What is a corrective action plan?
A corrective action plan (CAP) is an important quality management tool for any business or supplier. A CAP is a method of documenting non-compliance issues, identifying their root causes, and capturing measurable, achievable solutions and realistic deadlines.
Why is a corrective action plan important?
A CAP is important because it:
- Highlights opportunities for improvement and allows for the development of corrective actions
- Enables the implementation of corrective actions immediately after the audit (even without the full report)
- Allows corrective actions to be tracked, managed, and monitored
- Promotes continuous improvement
When applied properly, the CAP can improve a company’s processes, procedures and management systems and bring about compliance with standards or requirements. It can also allow businesses to strengthen and improve working conditions throughout their supply chains, which ensures a strong relationship with buyers.
How to implement a corrective action plan
A corrective action plan can provide a well-documented means of problem-solving and long-lasting change, which in turn can form a disciplined, practical implementation of the actions. Therefore, it is important to confirm that the required tasks in the CAP are carried out and documented.
Once you receive your corrective action plan, you will be able to see what the non-compliance issues are, these can be used to help determine the root cause.
This in turn will determine the corrective and preventative actions. For example, if the non-compliance was that first aid supplies are out-of-date, the immediate corrective action would be to replace those supplies with in-date items.
The long term corrective actions will be dependent on the root cause, i.e. why did this happen? It could be nobody has been tasked with checking the first aid kit, it could be that the person who has been assigned this task hasn’t been trained, it could be that the person is on sick leave and there is no backup person to check these, or it could be something else. In this case, the long term corrective action could be to train someone and perform internal audits to check the first aid boxes, this would help to determine if the training was effective.
It is important for operations to measure and assess the effectiveness of the corrective action after a specified period of time. Therefore, if the above mentioned internal audit was carried out this could highlight any potential issues. Another critical part of keeping a corrective action plan on track is thorough documentation and well-tracked communication.
Following these steps as laid out in the corrective action plan can take your business down the path towards compliance for its next audit.
Find out more about how our expert auditors can help your business or factory remain compliant with industry requirements.




© Eurofins Assurance 2025 Personal data protection policy