BRCGS Global Standard Packaging Materials
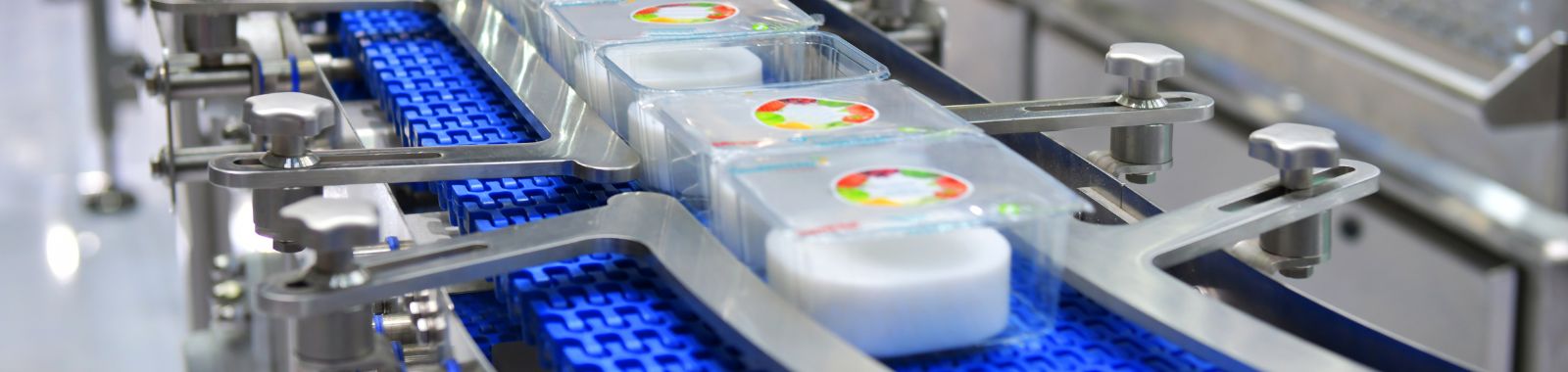

The BRCGS Global Standard for Packaging Materials is a well-recognised standard in the packaging industry for safety, quality, and legality of packaging products worldwide. The new version of the Global Standard Packaging Materials (Issue 7) was published on October 28, 2024. Audits for this updated standard will commence on April 28. Issue 7 brings significant changes and updates to the standard. Discover the key improvements and how they affect your operations by reviewing the detailed list below.
BRCGS certification is delivered by Eurofins Food Safety Solutions Limited in UK or Eurofins Certification SAS in France. You can check our accreditation qualification for UK here, and for France here.
Key changes BRCGS Packaging Materials Issue 7
Terminology changes
Global Standard Packaging Materials Issue 6
Staff, employees, personnel
Production
Intermediate
Company, Site
Packaging
Subcontracted activities
Global Standard Packaging Materials Issue 7
Personnel
Manufacture
Work in progress
Site
Product
Outsourced products
Section 1
- Items related to product safety and quality culture have been updated. Additions were made to some of the articles of Section 1 on product safety and quality culture regarding the importance of the issues related to product safety, legality and quality (such as inclusion in the policy, inclusion in the management review process agenda, presence of senior management on site during the audit to discuss issues related to product safety and quality culture ...)
- Added confidential reporting system requirement on issues related to product safety, legality and quality.
- The option of unannounced blended audits has been added, and responsibilities have been clarified for unannounced audits to be carried out in a timely manner.
- An article has been added that external expert / technical expert support can be obtained on issues related to product safety, legality and quality.
Section 2
- In the BRCGS Packaging Materials I-6 standard, only item 2.2 was a fundamental requirement, while in the BRCGS Packaging Materials I-7 standard, all of section 2 has been made a fundamental requirement.
- Section 2 has been revised in accordance with GFSI and Codex Alimentarius.
Section 3
- Specification requirements are included for cases where the material has a functional impact on the safety of the final product.
- Spreading internal audits over the whole year has been added.
- Implementation of corrective and preventive actions revealed during internal audits are detailed.
- Supplier evaluation and performance monitoring processes have been elaborated.
- Outsourced processes have been clarified and their inclusion in service specifications, supplier evaluation processes and HARA plans has been emphasised.
- A new requirement has been introduced that in the event of a significant event concerning product safety or legality, the site concerned must inform the current certification body within 3 working days.
Section 4
- New clauses and details have been added for doors, floors, walls and ceilings on site.
- The clause for water used in production processes has been detailed.
- Items related to product defence have been elaborated on monitoring, corrective and preventive actions and system review.
- The specification requirement has been elaborated in the equipment purchase clause, and new requirements have been added regarding the new equipment commissioning process and the storage of out-of-use equipment.
- A requirement for annual review of environmental monitoring programmes has been added.
- Two new sub-clauses (4.9.4 & 4.9.5) on allergen management and other physical contaminants have been added.
Section 5
New clauses:
- 4.6 - Procedure requirement that determines the status of the product and the actions to be taken in case of equipment failure
- 4.7 - Ensuring product conformity with customer requirements
- 4.8 - Storage of product samples in accordance with customer requirements
- 4.10 - Control of out-of-scope products, materials and areas
- 5.2 - Determination of the accuracy of the measuring equipment with respect to the controlled product parameters
- 6.2 - Verification of inspection and test procedures
Section 6
- Spelling changes were made in the clauses and no new clauses were added.
- The assessment of requirements according to risks related to production and based on the intended end use of the finished product is emphasised.
Section 7
- HARA plan requirement for commercial products and supplier approval/monitoring processes (including traceability testing) have been added.
Audit options:
- Announced Audit: documentation and Operations full audit (on-site) and 1 unannounced audit within 3 years
- Blended Audit: Documentation (remote), Operations (on-site) and 1 unannounced audit within 3 years
- Unannounced (Voluntary): Documentation and operations full audit (on-site)
Benefits of obtaining BRCGS Packaging Materials certificate
Obtaining the BRCGS Packaging Materials Certification offers several significant benefits, including:
- Consumer safety assurance: protects consumers from potential hazards associated with unsafe packaging, thereby enhancing public trust in your brand and products
- Regulatory compliance: BRCGS certification helps companies meet and often exceed legal requirements related to packaging materials.
- Enhanced market access: certification opens up new opportunities in the market by meeting globally recognized standards, as many leading retailers require BRCGS certification from their suppliers.
- Operational efficiency: attaining BRCGS certification often leads to improved operational practices and increased efficiency by aligning to well-recognised standards and practices.
Our certification activities are provided by independent companies and separate from consulting activities. Such services are also presented and sold to clients separately, not in bundle or packaged format. Impartiality is safeguarded by Eurofins Assurance’ relevant policies to avoid conflicts of interest.




© Eurofins Assurance 2025 Personal data protection policy